Our versatile mixed-picking solution, HaiPick System 2 achieves all the benefits of System 1 — with added bulk, palletized, and mixed-type storage capabilities.
System 2 integrates automated bulk and palletized goods handling with each-picking for order fulfillment, improving warehouse efficiency by up to 6x. This solution reduces touchpoints for mixed-picking operations and streamlines processes while maintaining the flexibility and scalability typical of HaiPick Systems.
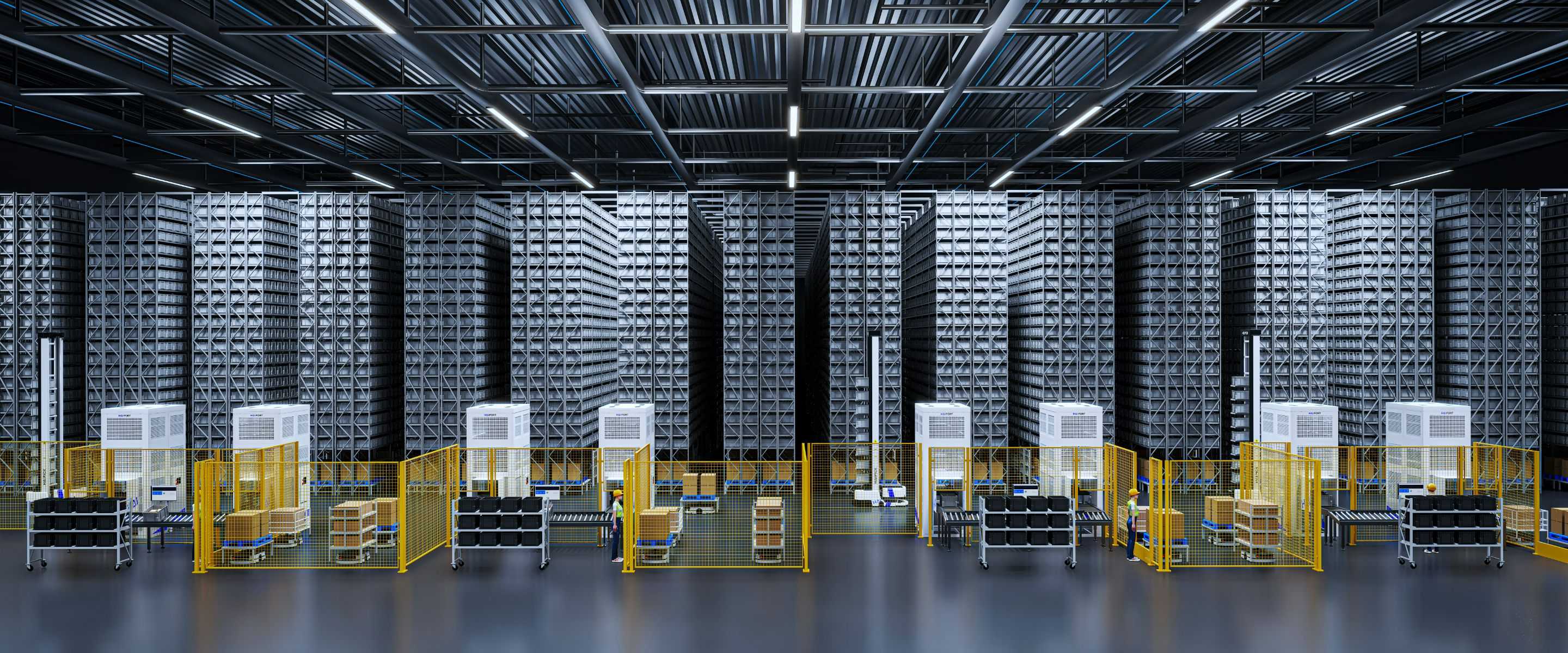
System 2 employs two types of robotic technologies to handle both bulk materials and individual totes or containers of goods. Autonomous Case-handling Mobile Robots (ACRs) strategically navigate confined storage zones, reaching up to 12 meters (39+ feet) high and 2 totes deep to transport inbound and outbound goods for storage and fulfillment. Simultaneously, Heavy-Duty Companion AMRs handle the picking of bulk and palletized goods.
Combined with other system features, each HaiPick System is tailored to meet the unique requirements of your application.
System 2 elements include:
- HaiPick Autonomous Case-handling Mobile Robots (ACRs)
- Heavy-Duty Companion AMRs for bulk and palletized goods picking
- Inbound/outbound workstations
- Industry-standard racking or shelving
- Any container, or no container for appropriate applications
- HaiQ software
Two core robotic technologies drive HaiPick System 2: Our Autonomous Case-handling Mobile Robots (ACRs) are designed to operate seamlessly with nearly any industry-standard racking and containers within a HaiPick System — enabling versatile and cost-effective goods-to-person operations. Meanwhile, Heavy-Duty Companion AMRs handle any material that fits on the robotic table.
Each robot is equipped with features tailored to the specific inventory it handles. Additionally, various models of ACRs can be employed within System 2 to enhance operational capabilities.
HaiPick Systems are accessed via workstations where inbound and outbound inventory is picked up and delivered by HaiPick Robots. Ergonomically designed, all workstations deliver a 99%+ order pick accuracy rate and can be tailored to maximize workflow efficiency and throughput, or facilitate seamless handoff to other technologies and operations.
Eliminate Human Travel for Order Picking
HaiPick Systems bring containers directly to operators, cutting out travel time for order picking and speeding up fulfillment.
Variable Workstations
Each HaiPick System can connect to different types of workstations operating simultaneously, supporting various workflows within a single system.
Lineside Delivery
HaiPick Systems deliver containers for manufacturing, kitting, and other processes through lineside delivery, conveyor systems, or other technology handoff points.
Safety
CE and NRTL certified.
HaiPick Systems can integrate seamlessly with almost any existing Warehouse Management System (WMS) or Warehouse Execution System (WES). HaiQ Software provides clear digital insights into inventory counts and details, optimizing robotic pathways to minimize travel and maximize order pick speed and efficiency.
HaiPick Systems are compatible with almost any industry-standard racking and shelving. Our HaiPick Robots are built to work within real-world tolerances, providing flexibility to manage inventory automatically without the limitations of traditional Automated Storage and Retrieval Systems (ASRS).
Any Rack
System 2 can operate with almost any racking type, provided there is enough clearance at the floor level to maneuver bulk items.
Any Container
HaiPick Systems are material-agnostic and can handle a wide range of containers, including totes, trays, cardboard boxes, styrofoam, metal baskets, and others of varying sizes.
No Container
For products that are appropriately sized and consistent, using a container may not be necessary.
What Makes a HaiPick System
To explore how a HaiPick System can advance your facility and connect with a local system engineer with experience in your industry, try our Solutions Generator.