Yonghui Logistics
Pengzhou Logistics Park

3x
Picking Efficiency

18,000
Storage Locations

10,000+
SKUs
-
High Labor Costs: Replenishment for B2B retail stores is characterized by high frequency, fast turnover, and diverse small-quantity SKUs. Offline stores often sync with online promotional events, leading to significant business fluctuations. Efficient warehousing and logistics are crucial to ensuring timely store replenishment and meeting diverse consumer needs. Traditional warehouse picking operations are heavily reliant on manual labor, making it challenging to control costs effectively.
-
Thoughput Bottlenecks: The current manual workflow limits efficiency. Employees must manage large-scale order reorganization across different areas, resulting in low average productivity of approximately 50 items/hour, which struggles to meet rapidly growing business demands.
-
Low Fulfillment Efficiency: The retail industry requires frequent and swift responses to diverse replenishment needs. During periods of surging orders, traditional picking methods fail to support efficient order fulfillment.
-
Insufficient Storage Space: With a massive SKU count and highly concentrated warehousing, traditional storage models are unable to adapt to fast-shifting categories and increasing dynamic demand.
By implementing automated solutions, Yonghui Pengzhou Logistics Center is able to provide efficient and professional replenishment support to over 100 stores across Southwest China, effectively addressing the above pain points and enhancing the long-term operational competitiveness of physical stores.
Addressing Yonghui's business scenarios and challenges, Hai Robotics engineers conducted in-depth discussions with Yonghui Logistics team members and ultimately decided to deploy the HaiPick System 1, a versatile and scalable Automated Storage and Retrieval System (ASRS).
This solution includes a complete set of hardware and software systems featuring ACR robots, HaiPort loading/unloading machines, and the HaiQ intelligent warehouse management platform, enabling full-process automation for inbound/outbound goods, piece-picking, and digital operations.
-
Storage density doubled, meeting multi-SKU storage needs for supermarkets
Compared to traditional manual racking, Hai Robotics' innovative solution offers racks nearly 4 meters high with 18,000 storage locations, accommodating over 10,000 SKUs in vertical storage. Post-upgrade, storage density was doubled, meeting Yonghui Supermarket's refined storage demands for a large number of SKUs.
-
Outbound efficiency increased by 3 times
After the project went live, the split-picking operations at Yonghui's Pengzhou Logistics Park in Sichuan achieved full-process automation for inbound, replenishment, inventory checking, and outbound processes, fulfilling both split-picking and full-case outbound workflows. During the inbound stage, it supports direct storage of original cartons without unpacking, allowing flexibility to handle business peaks. In the 4,500-square-meter second-floor warehouse, Hai Robotics divided the space into three small zones that cover all product categories. When picking orders are issued, robots can fetch items nearby and deliver them to the nearest workstation for outbound processing, eliminating the need for workers to go deep into the storage area for picking. Through this human-machine collaboration model, Yonghui Logistics' split-picking efficiency has increased by 3 times, enabling it to successfully handle peak periods such as the Chinese New Year, 618 Shopping Festival, and Singles' Day. Additionally, the more precise split delivery service helps stores reduce inventory turnover rates.
After multiple efficiency tests, we've found that the HaiPick System, with tote boxes as the core carrying container, meets our business needs for high SKU variety, small-sized products, high outbound demands, and the flexibility to handle order volume peaks and troughs.
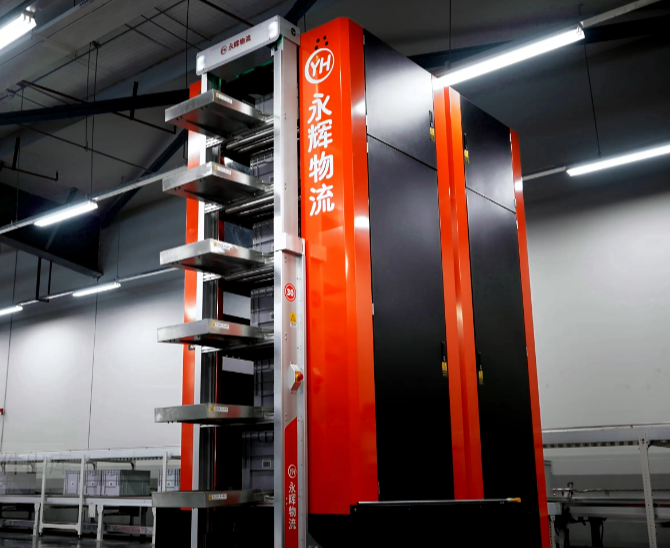
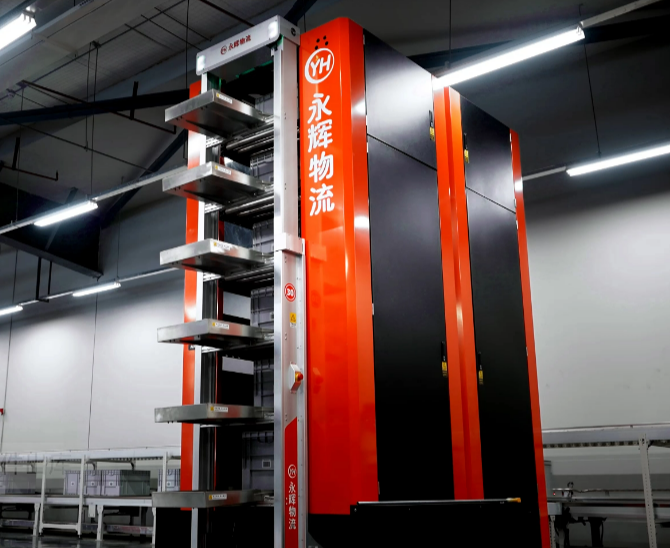
After multiple efficiency tests, we've found that the HaiPick System, with tote boxes as the core carrying container, meets our business needs for high SKU variety, small-sized products, high outbound demands, and the flexibility to handle order volume peaks and troughs.