Xin Hee (JORYA)
Automated Apparel Logistics Center

51,384
Storage Locations

90%
Warehouse Utilization Rate

35 cases
Per Hour for Each Robot

Intelligent
Smart algorithm Schedule Robots
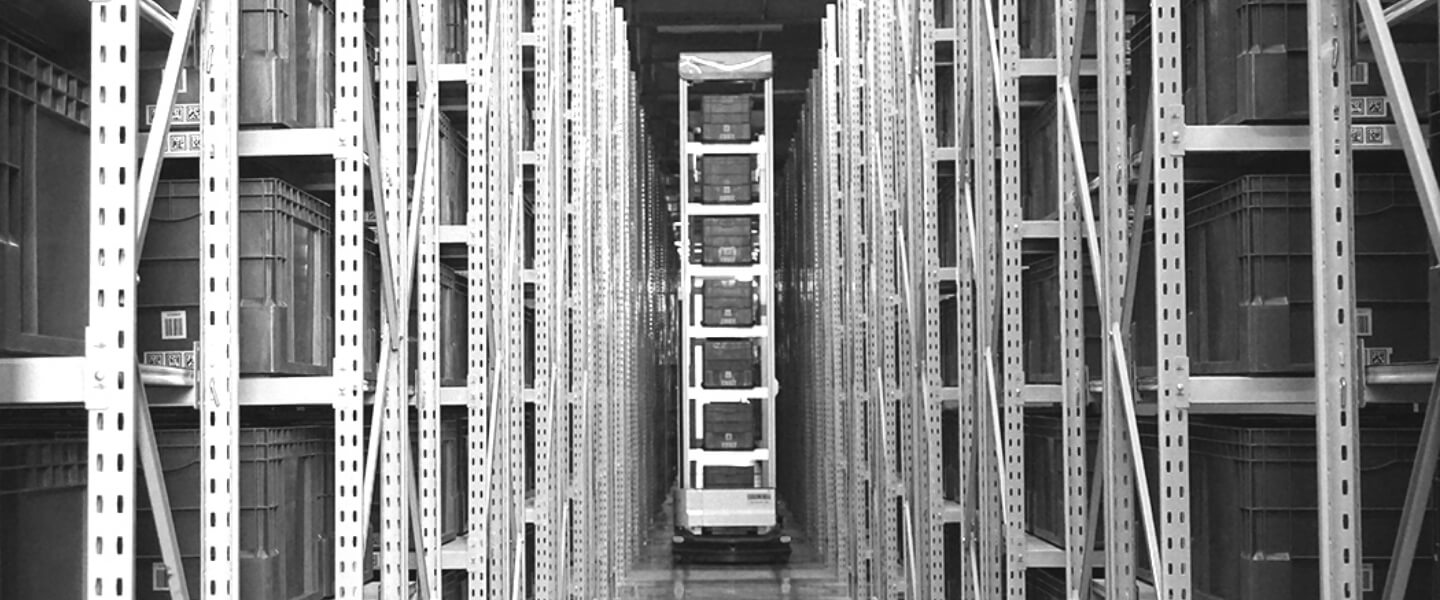
Xin Hee is building a large-scale automated logistics center in Tong'an, Xiamen. The logistics center has 6 floors. HAI ROBOTICS helped transform the case picking area (floor 3 and 4) into an automated logistics management warehouse for 2B and 2C goods with high efficiency and quality. The project introduced 34 customized HAIPICK A42 robots, 14 U-shaped conveyor workstations, 12 charging stations, and the HAIQ Software Platform. The project has realized a shelving area of 6,200 square meters and has provided more than 50,000 storage spaces.
1. HAIPICK robots improve manual work and the process of placing and handling cases
34 customized HAIPICK robots shuttle through different floors (floor 3 and 4) quickly, according to the instructions, carry out case storage, handle, and sort accurately, improving manual work. The 5,000 square meters warehouse only needs 7 workers to sort goods in the workstation area, saving the labor cost and significantly improving manual operation.
2. Rational planning, warehouse storage utilization reaches 90%
HAI ROBOTICS' scheme plan uses 1,706 sets of shelves, providing a total of more than 50,000 storage spaces and realizes the storage of 8 customized cases per square meter. HAIPICK robot is 4.5m high, making the warehouse utilization rate as high as 90%.
3. Perfect case-to-person design to meet the needs of efficient storage warehouse
The efficient case-to-person solution makes the picking and transportation path of the HAIPICK robot smooth, reduces waiting time, and avoids congestion, realizing 35 cases per hour for each robot.
4. Seamless connection with WMS system to optimize the location, path, and task allocation
HAIQ can seamlessly connect with Xin Hee's WMS intelligent warehouse management system. After receiving the task instructions from WMS, it can optimize the algorithm according to the storage situation of goods, reasonably plan the warehouse location and path, and efficiently schedule the robot to complete the operation of picking and placing cases.
5. Optimization of human-machine interaction
HAI ROBOTICS designed double-layer U-shaped conveyor workstations. The upper layer is the U-shaped picking case conveyor line, and the lower layer is the order box conveyor line. It can realize the operation of placing sorting, returning, and outbounding cases simultaneously. The design improves the comfort and practicality of manual operation.
6. Customized robots and totes to better meet customers’ needs
The maximum height of the customized HAIPICK robot for this project was 4.5m, and the net height suitable for the warehouse was 5m. The size of totes and charging stations were adjusted according to the size of the robot; besides, the robot and charging station's exterior color was customized according to the brand color of Xin Hee.
7. Flexible and expandable to meet the demand during peak periods and business development
In the case of future growth, the solution can expand the number of robots and charging stations to meet the needs of the company's development.
"In the future, we look forward to realizing more warehouse automation innovation in cooperation with Hai Robotics."
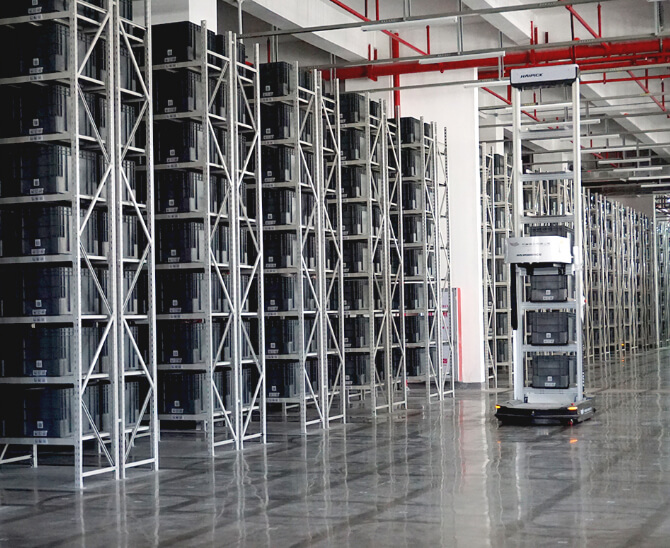
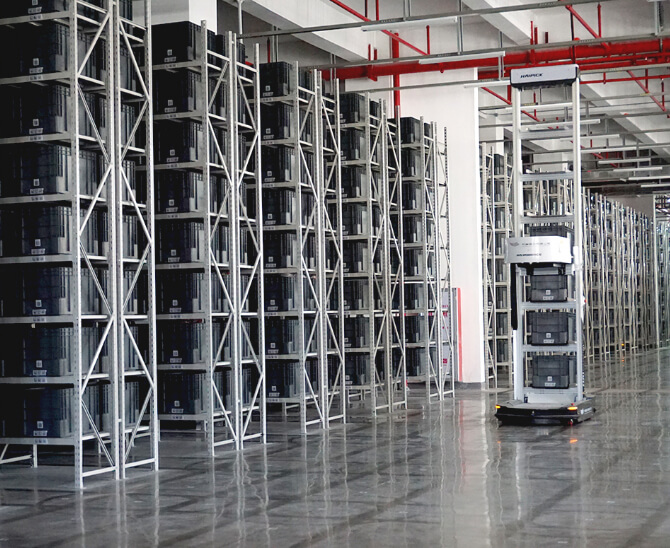
"In the future, we look forward to realizing more warehouse automation innovation in cooperation with Hai Robotics."
Downloads

Download our latest industry report and learn how ACR powers different sectors. You'll learn exactly what ACR is and why it's different and so powerful.

Download the white paper and discover what industry leaders think about the future of warehouse automation, the impact it would have on workforces and sustainability, the risks facing the industry, and the potential avenues for collaboration to drive forward progress.