SENCO Příbram
Electronics Warehouse

6,879
Storage Locations

9,360
SKUs Managed

51 totes/hour
Inbound Throughput (double cycle)

13 totes/hour
Outbound Throughput (double cycle)
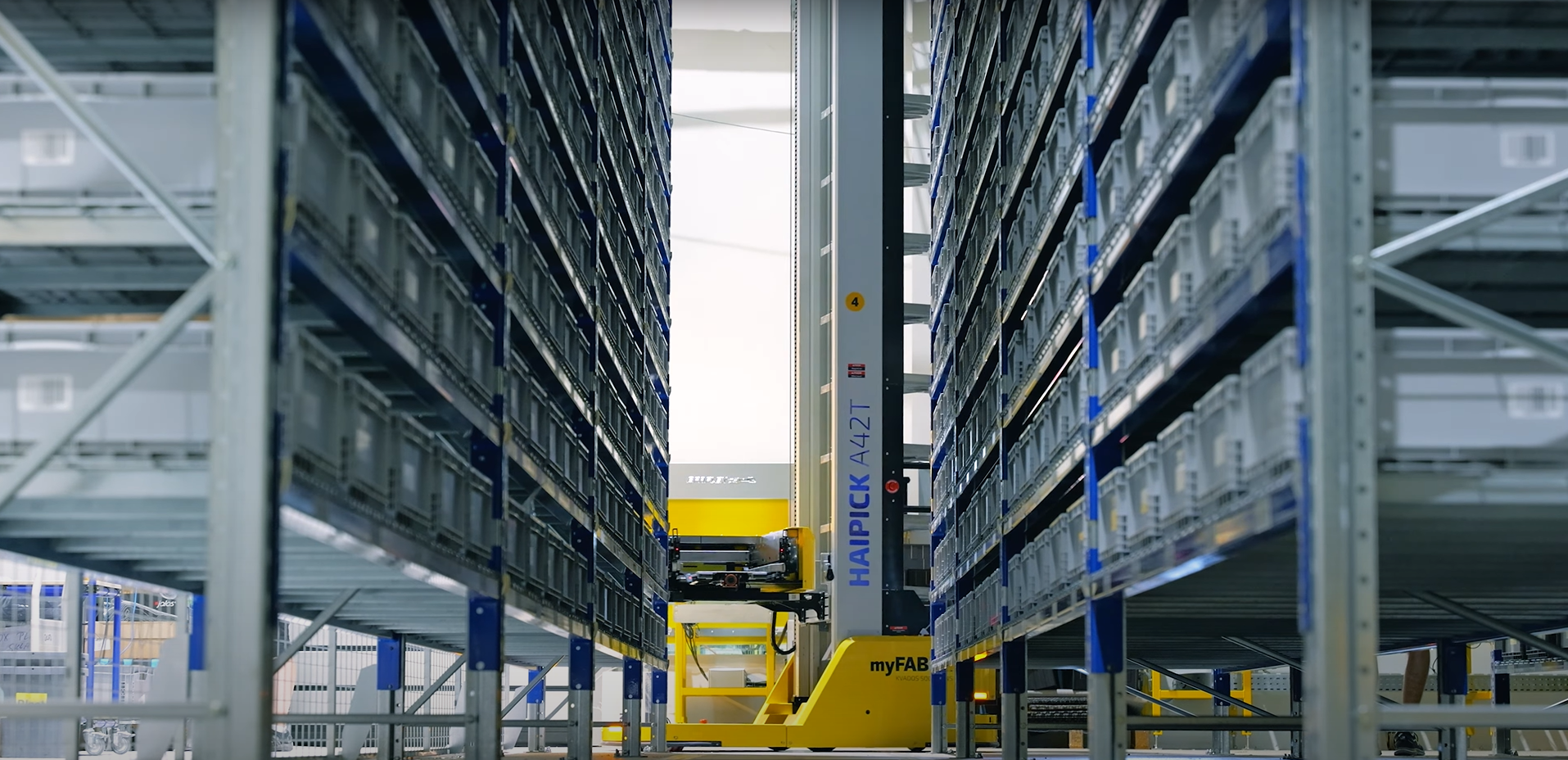
-
Limited storage capacity, with SKUs exceeding available locations.
-
Inefficient use of vertical warehouse space.
-
Manual processes for receiving, replenishment, and tote identification.
-
High error rates due to paper-based operations.
-
Rising labor costs, persistent labor shortages, and extensive training needs.
-
Optimized Storage: Deployed 4 HaiPick A42T robots, designed for single-depth racks and 10-meter-high storage. This configuration maximized space and allowed efficient management of 6,879 locations for 9,360 SKUs.
-
Streamlined Processes: Implemented conveyors with docking points for inbound and outbound operations, simplifying workflows for receiving, replenishment, and tote release.
-
Improved Efficiency: Automated stock-taking and inventory management, reducing manual errors and improving accuracy.
-
Custom Fit Technology: Plastic totes (600x400x170 mm) tailored to the system, ensuring seamless compatibility and scalability for future needs.
Download your copy to access key takeaways
