Philips Zhuhai
Smart Household Appliance Factory

8 Cases
Storage Density Per Square Meter

130 Cases
Outbound/Inbound Efficiency Per Hour

99.99%
Picking Accuracy

2,466
Storage Locations
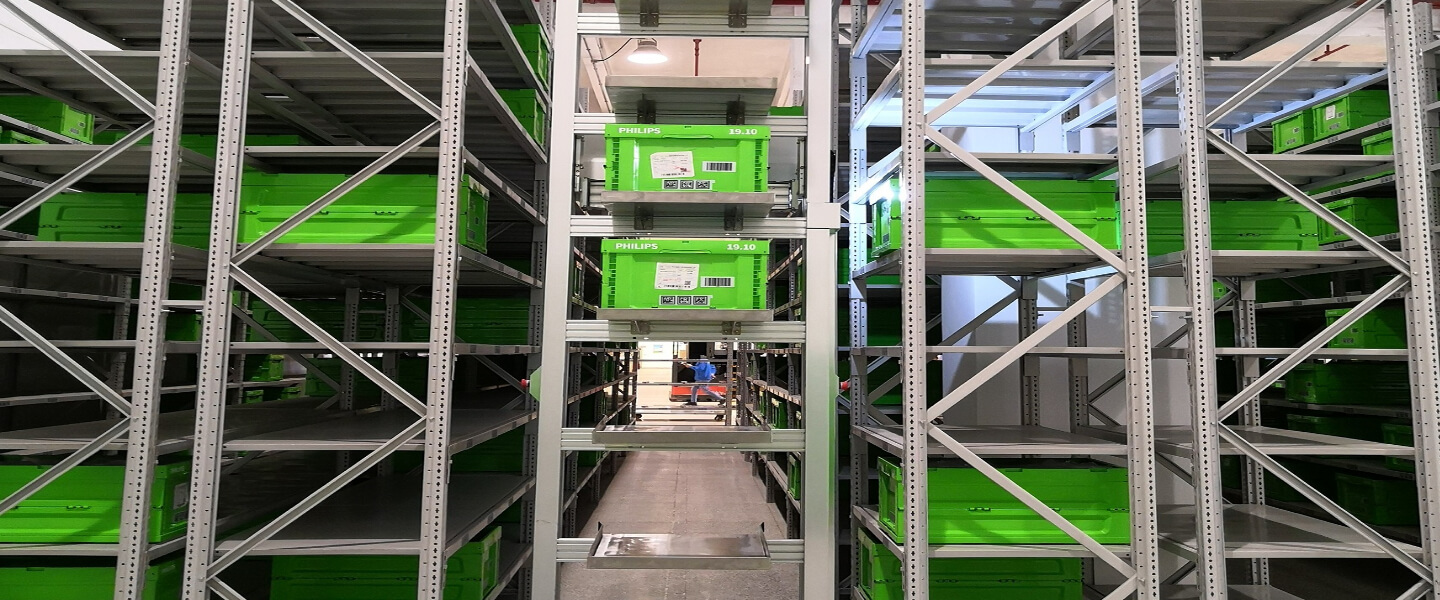
In recent years, Philips Zhuhai's home appliance factory's demand for intelligent warehouse transformation has become increasingly urgent. The customers hope to increase picking and handling efficiency through automation transformation and realize intelligent inbound and outbound warehousing processes with data-based and information-based warehousing management. The project introduced multiple HAIPICK A42 robots, conveyor workstations, buffer shelving workstations, and put to light system for automation transformation to meet the feeding needs of numerous production lines, and completed the standardization of case turnover and the use of QR codes.
1. Intelligent split orders to meet different business needs
The HAIQ Software Platform transformed paper-based management to digital and information management. It realized storage by areas, strictly following bonded and non-bonded commodities' attributes to carry out inventory management, storage management, intelligent split orders, and deliveries, reducing manual errors, and reaching a picking accuracy of 99.99%.
2. An efficient case-to-person solution to improve human efficiency
HAIPICK robots replace manual labor to carry out efficient picking and handling. One worker can perform tasks that would otherwise be done by 2-3 workers, satisfy the feeding demand of multiple production lines, improve the human efficiency, and significantly saves the workforce and cost.
3. Rational planning to realize a flexible storage warehouse process
HAIPICK robot intelligently identifies incoming warehousing components and parts, carries out handling and storage, and connects with the conveyor line to realize flexible warehousing. The storage area is equipped with buffer shelving workstations and put to light system, which flexibly supports various methods such as separate picking and whole case picking, saving waiting time, and realizing flexible and smart warehousing.
4. Creating Philips intelligent logistics standardization
The warehouse system unifies the standard case turnover and standardizes the use of QR code labels, reduces the consumables and logistics cost, and realizes logistics information standardization. This pilot project is the first intelligent warehouse transformation for Philips Group, pushing forward its construction of a standard and intelligent logistics system worldwide.
"In the future, we will carry out more in-depth cooperation with Hai Robotics to build a benchmark for smart factories and enable intelligent manufacturing."
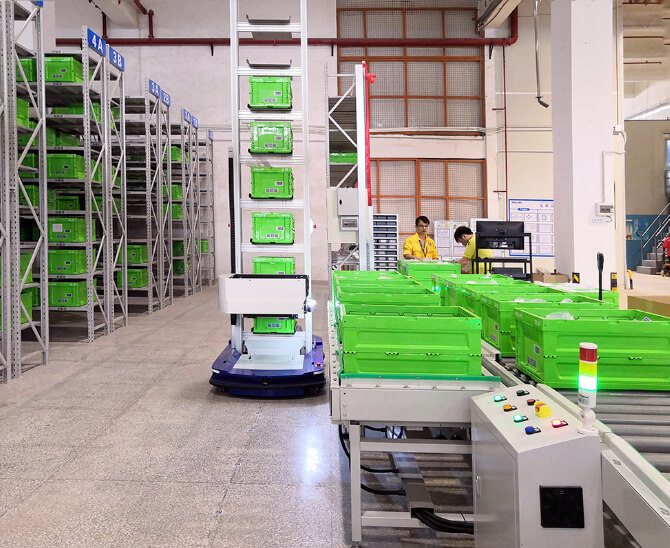
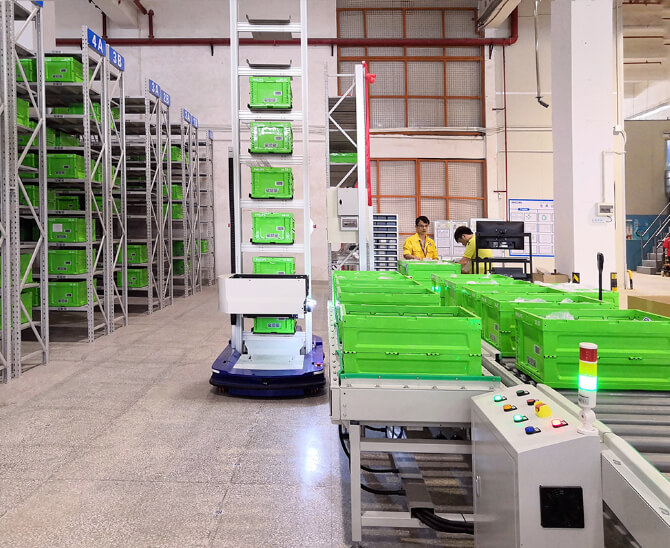
"In the future, we will carry out more in-depth cooperation with Hai Robotics to build a benchmark for smart factories and enable intelligent manufacturing."
Downloads

Download our latest industry report and learn how ACR powers different sectors. You'll learn exactly what ACR is and why it's different and so powerful.

Download the white paper and discover what industry leaders think about the future of warehouse automation, the impact it would have on workforces and sustainability, the risks facing the industry, and the potential avenues for collaboration to drive forward progress.