Geely LYNK&CO
Assembly Shop KLT Warehouse

43,966
Storage Locations within 3,300㎡

100 totes/h
Conveyor Inbound Workstation Efficiency

600 totes/h
Fast-inbound Workstation Efficiency

99.9%
Picking Accuracy
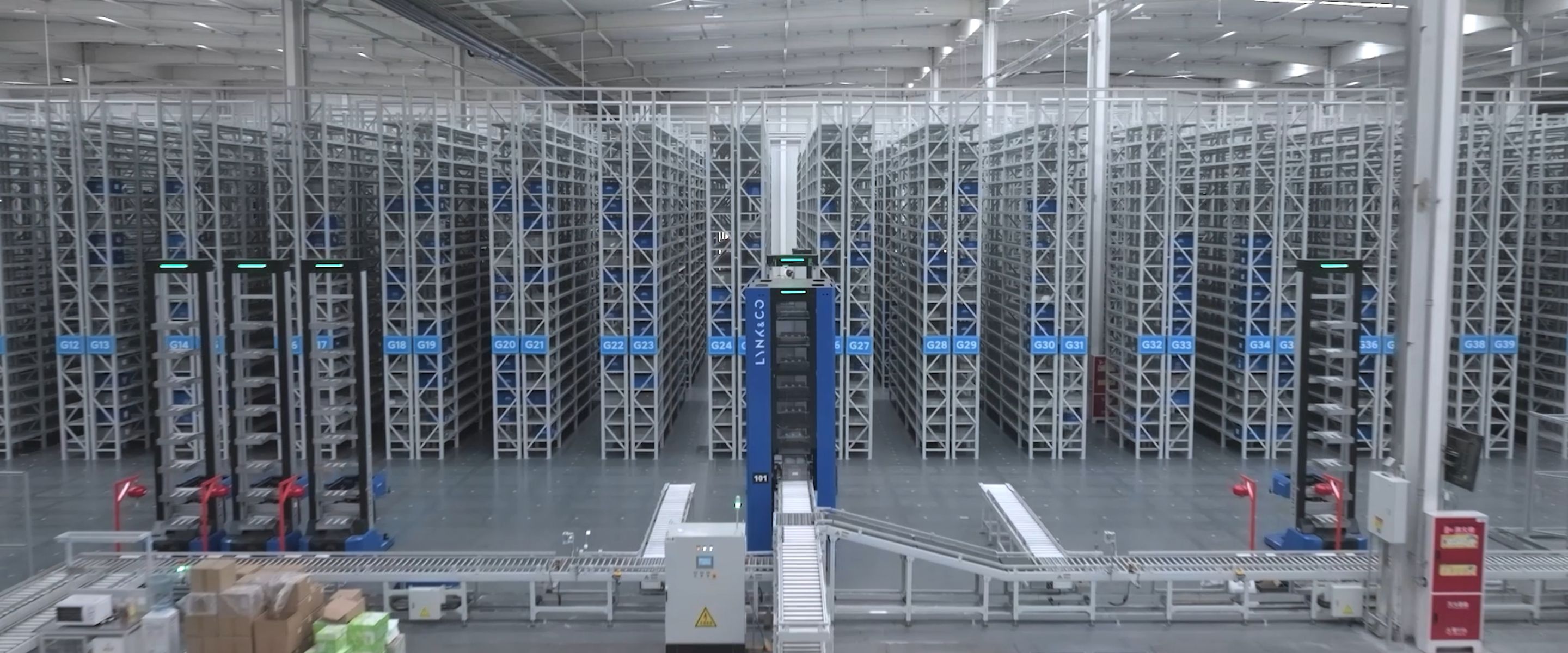
--The increasing amount of substantial manual handling and manual identification.
--Long working hours and high labor intensity.
--Inaccuracies causing problems with outbound operations.
--Difficulties in recruitment and issues with unreliable personnel.
--Robot quantity & type: 31 units of A42T
--Workstation type & quantity: 2 sets of HaiPort workstations, 6 sets of buffer rack workstations, and 2 sets of conveyor workstations.
--Shelving height: 7,900mm
--Storage unit type/size: Totes 800mm(L)*600 mm(W)*280 mm(H); 600mm(L)*400mm(W)*280mm(H); 400mm(L)*300 mm(W)*280 mm(H); 300mm(L)*200 mm(W)*280 mm(H)
--Warehouse area: 3,300㎡, achieving 43,966 storage locations.
--Achieved over a 99.99% accuracy rate, which improved performance efficiency.
--Conveyor inbound workstations reached a new maximum process rate of 100 totes per hour.
--Fast-inbound workstations can effortlessly meet the needed demand of 600 totes per hour.
--Both workflow and transportation efficiency were tremendously improved thanks to the Haipick which can retrieve up to eight totes at a time docking seamlessly with the HaiPort.
--The warehouse successfully fulfills the simultaneous production of multiple car models by replacing traditional low rack storage with a towering vertical storage system and with the added flexibility of six different types of totes for various types of components.
"The use of Hai Robotics’ ACRs has greatly improved the efficiency of warehouse picking. Geely achieved a more refined management of multiple SKUs and met the factory's just-in-time production requirements. Additionally, the high utilization of storage space further increased the storage density."
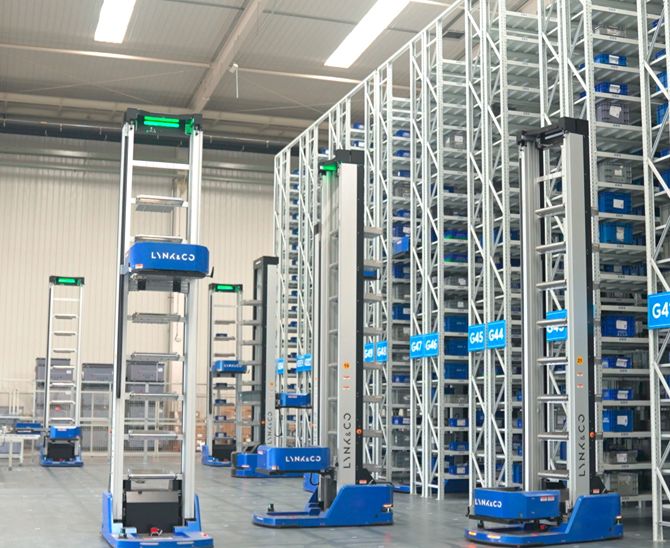
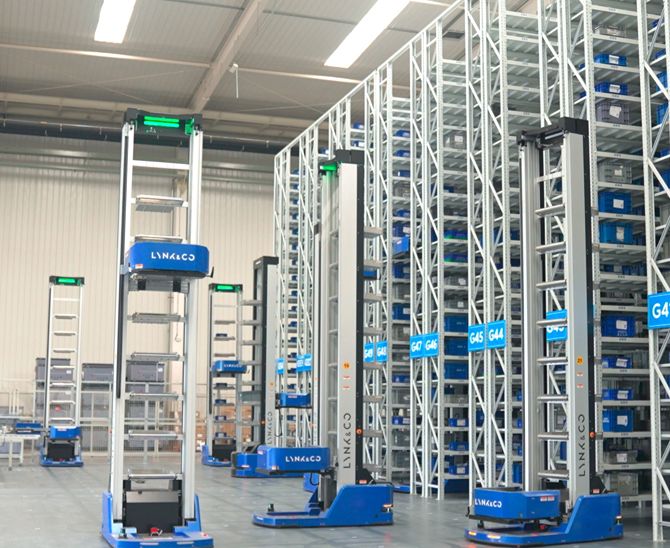
"The use of Hai Robotics’ ACRs has greatly improved the efficiency of warehouse picking. Geely achieved a more refined management of multiple SKUs and met the factory's just-in-time production requirements. Additionally, the high utilization of storage space further increased the storage density."
Downloads

Download our latest industry report and learn how ACR powers different sectors. You'll learn exactly what ACR is and why it's different and so powerful.

Download the white paper and discover what industry leaders think about the future of warehouse automation, the impact it would have on workforces and sustainability, the risks facing the industry, and the potential avenues for collaboration to drive forward progress.