Bosideng
Intelligent Distribution Center
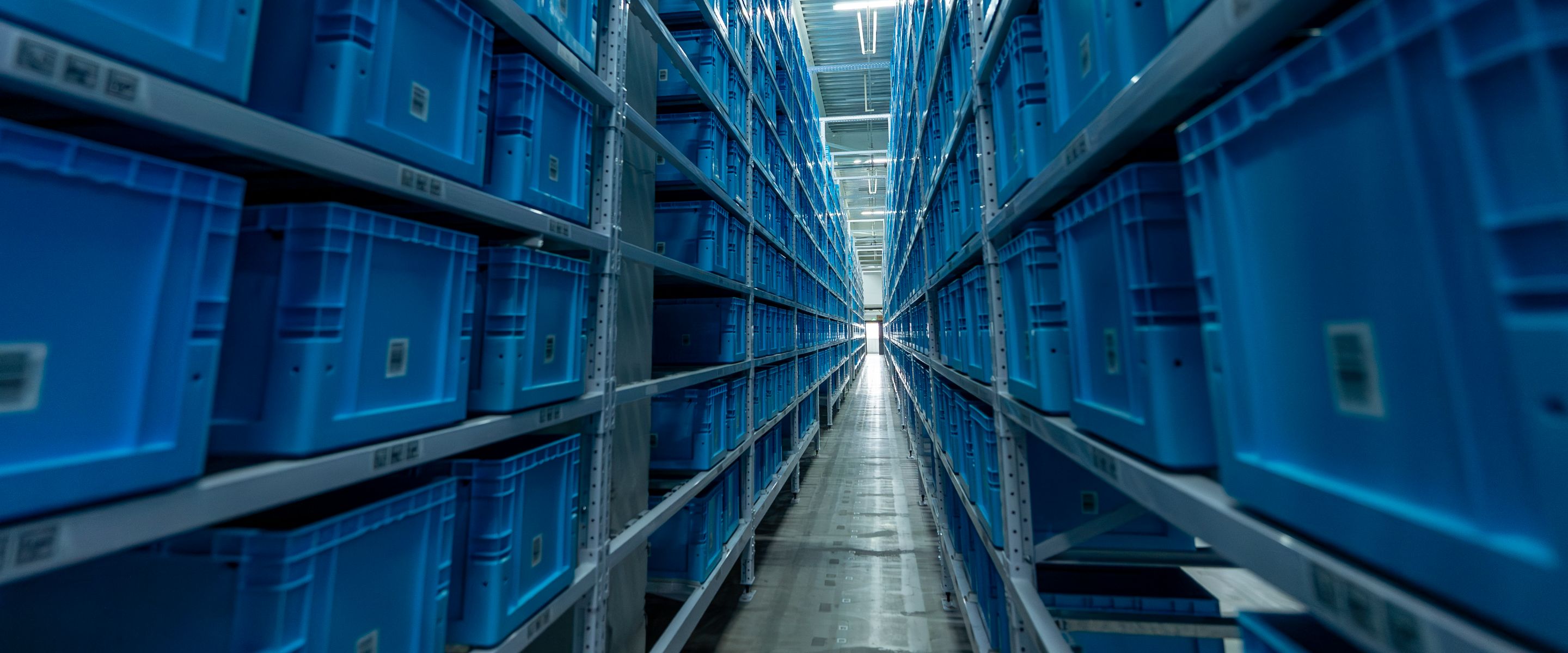
The Bosideng Group Logistics Park (Intelligent Distribution Center) spans approximately 150,000 square meters, with a total construction area of 184,000 square meters. After successfully operating the HaiPick System 1 for two years, the company decided to further adopt the HaiPick System 3 to meet its growing business demands.
The project warehouse spans an area of 7,665㎡ with a net clear height of 5.7 meters, and a storage height of 5.4 meters, allowing full utilization of the vertical space. The warehouse accommodates a planned total of 69,274 storage locations and uses Bosideng’s standardized totes or cartons measuring L600*W400*H400 for storage. The total storage capacity reaches 260,000 items, achieving a storage density of 8.44 boxes per square meter.
Hai Robotics implemented the HaiPick System 3 for the facility, deploying 61 ACRs and 219 AMR K50s, supplemented by 4 inbound workstations and 12 outbound workstations. The ACR robots use clamp-style forks, enabling flexible handling of totes and cartons of varying dimensions.
For inbound operations, the cartons are swapped into totes at the workstations. Then, AMR transport the totes to temporary storage racks at the bottom of the shelving system. ACR pick up the totes from this area and lift them to high shelving locations to complete inbound storage.
For outbound operations, ACR retrieve items from high shelving and place them on the temporary ground-level shelves. At this point, AMR take over and transport the items to the outbound workstations. Items are prepared at picking workstations, after which completed order totes are consolidated via conveyor belts and transferred to spiral elevators that deliver the totes to the first-floor sorting and packing area.
By coordinating the efforts of ACR and AMR, the solution boosts outbound efficiency to 2.5 times the pre-deployment level. Outbound processing now achieves a rate of 3,600 lines per hour, while inbound processing reaches 1,400 totes per hour.

99.99%
Picking Accuracy

69,274
Storage Locations

2.25x
Storage Density

100,000+ items
Outbound in Peak Season
HaiPick System 3 fully meets the annual capacity needs of the warehouse and provides flexible capacity expansion. They can adapt to different operational scenarios such as daily shipments, small-scale promotions, and large-scale promotions with compatible system mechanisms.
To handle peak orders from November to February and March to April, this warehouse is primarily used for processing B2C hot-selling products. The daily average number of shipments throughout the year reaches 36,584 pieces, ensuring no pressure during business peaks.