How Warehouse Robots Enhance Workers' Safety
Warehouse management plays a pivotal role in the smooth operation of supply chains, with primary emphasis on maintaining a safe workspace for all employees. Safety has already transcended its role as merely a legal requirement; and the reason is warehouse operations' success and sustainability.
Since warehouse safety has become increasingly paramount, companies have increasingly turned toward warehouse automation to help accomplish safe warehouses. The adaptation of automated warehouse robots not only revolutionizes warehouse function, but dramatically improves safety and efficiency. Now, let's explore how automated warehouse robots are enhancing employee safety:
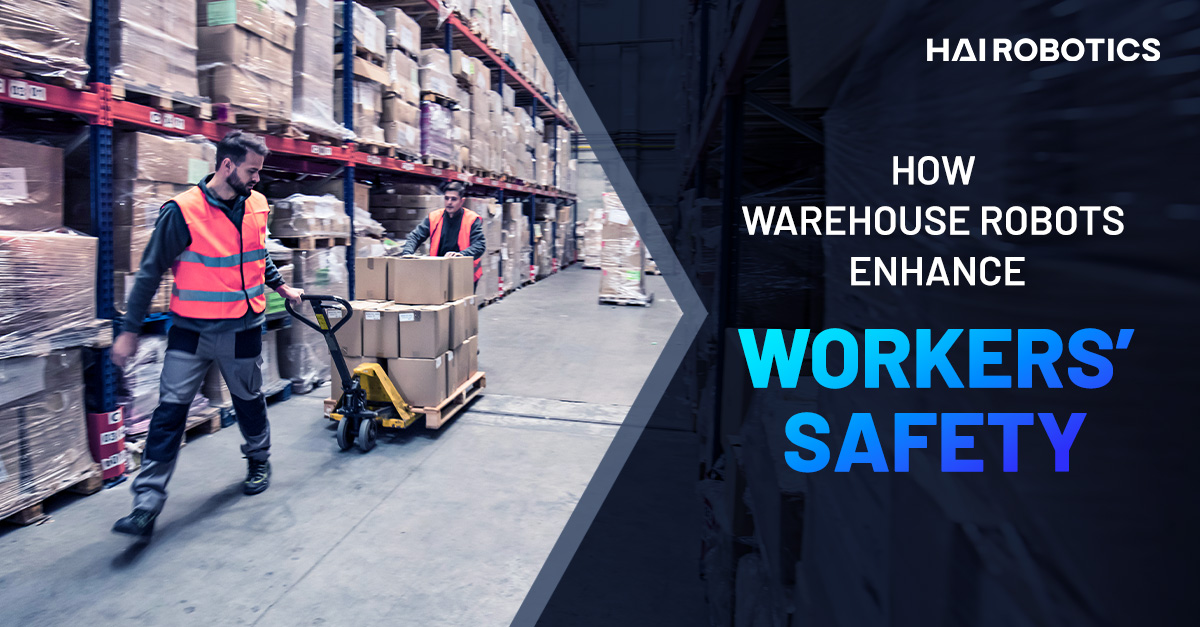
1. Reduce physical strain and injuries
Manual labor in warehouses often involves physically demanding tasks, such as lifting and moving heavy loads, which can lead to musculoskeletal injuries over time. Automated warehouse robots are quite adept at handling these tasks, thus reducing the risk of strains, sprains, and other ergonomic injuries among workers. By managing duties such as lifting and transporting heavy items, warehouse robots significantly reduce the risk of injuries caused by physical strain.
Take Hai Robotics' Autonmous Case-handling Mobile Robots (ACRs), for example. With multiple storage trays, a single ACR can handle up to nine cases simultaneously. The maximum weight for these cases can reach 270kg, significantly more than a human worker can handle. In addition, ACRs can move these hefty loads in much safer ways.
In many manually operated warehouses, employees have reported to work long hours doing monotonous, repetitive tasks under stringent deadlines. This can lead to worker fatigue and increase the likelihood of errors. Numerous injuries can occur as a result of human errors. By using warehouse robots, which don’t have a sense of urgency or fatigue, companies can reduce the risk of injuries caused by human error and worker fatigue.
2. Collision Prevention and Reduced Accident Risk
Accidents involving traditional material handling equipment, such as forklifts and pallet jacks, pose a significant safety concern in manual warehouses. However, in automated warehouses, robots operate with precision and accuracy, following predefined paths and adhering to strict safety protocols. These robots are equipped with sensors that can detect obstacles and successfully navigate around them, reducing the risk of accidents caused by human error and improving overall warehouse safety.
In an automated warehouse that uses the HaiPick system, numerous safety measures are in place. These include guard doors, safety fences, interlocked locks, electrical cabinets, warning lights, and button switch boxes.
The robot operating zone is demarcated from human workspaces by a safety fence and guard door, which minimizes direct contact between personnel and mobile robots. Access to the robot operating zone is limited to authorized personnel only, through a guard door equipped with an interlocking lock. This lock halts all operations while the guard door is open. Such basic safety systems offer employees working in automated warehouses a high level of protection from accidents and collisions.Certain warehouse tasks pose inherent risks to workers, such as working at heights or handling hazardous materials. Robots excel in automating these tasks, reducing human exposure to potentially dangerous environments.
This strategic use of automation not only enhances safety but also optimizes workflow efficiency. To improve storage density, warehouse management should utilize the vertical space of the warehouse as much as possible, but this increases the risk of falls. Warehouse robots can safely load and unload items that are too high up for human workers and keep them far away from potential falls. Hai Robotics' ACR robots, for example, can pick and store plastic totes and carton boxes at dizzying heights of up to 12m, which increases warehouse storage density and enhances warehouse safety.
3. Improved Ergonomics
Repetitive bending, lifting, and reaching can lead to ergonomic strain and discomfort for workers. Automated robots optimize ergonomics by performing these tasks efficiently and without physical strain. By reducing the need for manual, labor-intensive activities, robots contribute to improved ergonomics and overall well-being among warehouse employees.
In a goods-to-person setup, for example, automation brings products directly to employees at ergonomically designed picking stations. Products arrive in plastic totes, crates, or bins, positioned optimally in terms of height and angle, enabling workers to pick required products with speed and ease. When an Autonomous Mobile Robot (AMR) carries a tote to a desktop workstation, the robot elevates the tote through the picking slot to a suitable height, enabling the worker to pick goods comfortably. This eliminates the need to bend down.
4. Automated Warehouse Comprehensive Safety Features
Many automated robots are engineered with comprehensive safety features and protocols. These may include collision detection systems, emergency stop buttons, and safety zones that restrict human access during operation.
Most are equipped with advanced sensors and cameras that enable monitoring of the warehouse environment. They can detect obstacles, identify potential hazards, and respond swiftly to changing conditions. For example, automated storage solutions can be integrated with fire suppression systems depending on the region and country the facility is located.
The warehouse automation safety solutions provided by Hai Robotics comply with safety regulations, and minimize the risk of fire-related incidents. By adhering to strict safety standards, robots ensure compliance and contribute to a culture of safety within the warehouse dependant on the region or country.
-
Emergency Stop: If a hazardous emergency occurs in the robot operating zone, this function can be used to halt all operations immediately. However, it is unsuitable for maintenance purposes as it causes robots to stop abruptly.
-
System Pause: If an issue occurs in the robot operating zone and personnel need to enter for troubleshooting or routine maintenance, this function can be used to swiftly pause all operations. Once triggered, personnel can enter through a safety door equipped with an interlocked lock. After maintenance is completed and personnel exit, operations can resume.
-
Fire Yielding: In case of a fire alarm, the system can receive corresponding signals, and all robots will immediately execute fire yielding instructions, giving way to firefighters or fire vehicles.
-
Green Passage: If needed, the system will automatically plan a green passage for maintenance personnel, starting at the safety door and leading to the designated location. All robots will execute yielding instructions once maintenance personnel enter. This function can be used in conjunction with the emergency pause function to enhance maintenance efficiency.
-
Safety Vest: This is a type of personnel protective equipment worn by maintenance personnel, equipped with a signal transmitter on the personnel side and a signal receiver on the robot side. Robots will execute yielding instructions based on a preset safety range with the operator as the center or even stop until the operator passes by if no path can be planned. This device can protect maintenance personnel and improve maintenance efficiency.
Conclusion
The adoption of automated warehouse robots signifies a significant step forward in enhancing workers' safety and well-being. By leveraging cutting-edge technologies, businesses can mitigate risks, improve efficiency, and prioritize the health of their workforce. As automated robots continue to evolve and integrate seamlessly into warehouse operations, their role in enhancing safety standards will remain pivotal.
Embracing these technologies demonstrates a commitment to safety excellence and positions businesses for success in a rapidly evolving industry landscape. Visit our page here to learn more about our systems and available safety features for your needs and location.