JD Logistics
California Distribution Center

The Solution
All shelving and totes were standard non-precision assets that are readily available on the market. This allowed the system to both be designed to best support the facility’s needs and avoid unnecessary costs. These ACRs are intelligent enough to work in real-world environments. The robots needed only standard configuration typical for all installations so robotic grippers match the tote size selected for the shelves.
Hai Robotics’ ACRs seamlessly integrated via a flexible interface communication layer with JD Logistics’ existing WMS system, helping to minimize the adjustment period to the new workflows and integration time.
60 Autonomous Case-handling Robots (ACR)
100,000+ SKUs Currently Managed
42,028 sqft (3,906 ㎡)
731 sets of shelves
32,428 tote locations
3 Inbound Workstations
6 Outbound Workstations
* Each with high efficiency double-in and double-out conveyors
* Each with 2, 15-tote put-walls (30 order fulfillment locations)
After Hai Robotics’ ACR system was implemented, JD Logistics’ picking efficiency was improved to 100% accuracy, significantly increasing their shipping precision. Ergonomic workstations that provided clear instructions and action prompts for the operators were implemented while automating repetitive tasks.
This system is designed to support up to 600 picks / hour / operator, equating to about 350 orders / hour / workstation resulting in a maximum of 2,100 orders from the system each hour.
Prior to the implementation of Hai Robotics’ ASRS, JD Logistics’ average hourly throughput was 451.6 outbound orders / hour. Compared to their new daily average of 641.7 outbound orders / hour - that is a daily order fulfillment improvement of 42.09% with Hai Robotics operating at about 1/3 of the system’s maximum performance capacity. The system’s flexibility and full capabilities are seen during peak season.
Throughout the year the system flexes with demand, more or fewer ACRs are deployed, and workstations come on and offline as needed. The range of the solution’s flexibility is best seen when the system is pushed to meet the extreme market demands during Black Friday Week.
The average number of orders fulfilled in a week with Hai Robotics is 44,919 . During Black Friday Week (Nov. 24 – 30) JD Logistics successfully fulfilled 98,156 orders with the same ASRS and no additional temp-staffing. This short-term increase in orders fulfilled is 118.52% over the normal weekly rate that the Hai Robotics’ system was able to easily flex and support.
Hai Robotics’ ACRs helped JD Logistics almost triple the number of orders they can fulfill for Black Friday. Before implementing Hai Robotics’ solution, JD Logistics fulfilled 35,745 orders during Black Friday Week. Compared to the 98,156 orders fulfilled for Black Friday Week after implementing Hai Robotics’ system - that’s an increase of 62,411 orders, or 174.6% more throughput JD logistics was able to fulfill during the busiest time of year.
Training has been significantly reduced from 8 hours of structured training and 2 weeks of supervised work throughout the facility, to a 2-hour training video and about 2 days supervised work at the workstations.
The role of order fulfillment has become less strenuous, helping to both lower turnover rate and expand the role to a larger hiring pool. Employees were previously walking 10+ miles a day to fulfill orders, after Hai Robotics ACRs were implemented, employees now pick in ergonomic, operator friendly workstations.
Hai Robotics ACRs allowed JD Logistics to increase their storage height from about 5 feet to 17 feet high, that’s an increase of 240% more vertical storage. Using the same storage footprint, the number of unique SKUs JD Logistics stores and manages in this facility has increased 42.9%, from 70,000+ SKUs to 100,000+ SKUs with room to grow – this allows JD Logistics to effectively take on new customers and provide more capacity to existing customers. Storage totes are organized and placed closely together, use of vertical space is maximized, and shelving unites are placed close together with minimal aisle space.
JD Logistics' California distribution center maximizes throughput and operational efficiencies with Hai Robotics' ASRS solution.
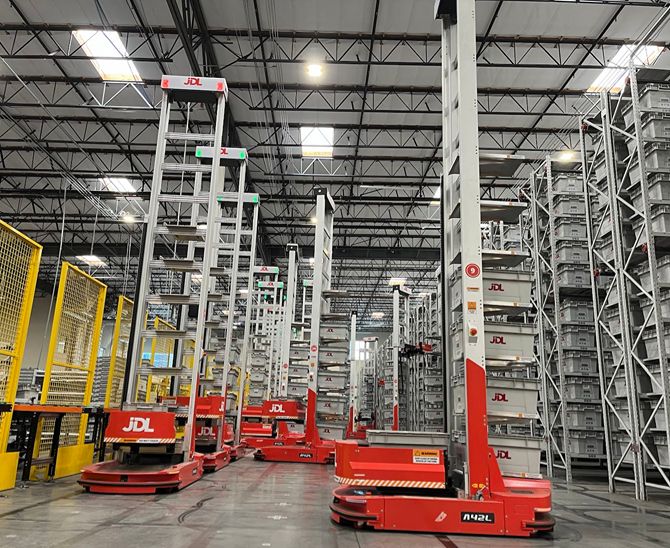
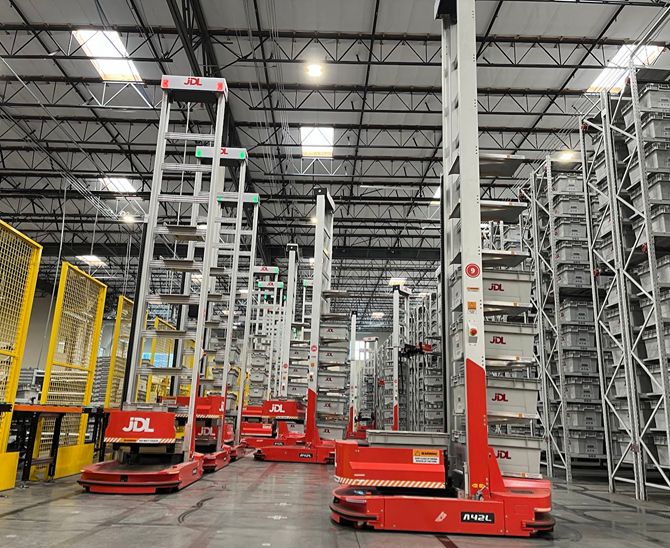
JD Logistics' California distribution center maximizes throughput and operational efficiencies with Hai Robotics' ASRS solution.
Downloads

JD Logistics’ California location upgraded its manual processes by implementing Hai Robotics’ Autonomous Case-handling Robotic (ACR) Automated Storage and Retrieval System (ASRS) to speed up order fulfillment, increase storage density, increase efficiencies, and improve inventory management.

Download our latest industry report and learn how ACR powers different sectors. You'll learn exactly what ACR is and why it's different and so powerful.

Download the white paper and discover what industry leaders think about the future of warehouse automation, the impact it would have on workforces and sustainability, the risks facing the industry, and the potential avenues for collaboration to drive forward progress.